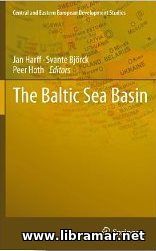
The present volume compiled by Jan Harff, Peer Hoth and Svante Bjorck, contains the results of a Special Symposium which was held some years ago and dedicated to the Baltic Sea basin with the purpose to foster the due understanding of it looking from the point of structure and genesis as well as processes and utilization issues.
The publication contains the comprehensive overview about the basin of the Baltic Sea, worked out by the scientists in the different relevant disciplines. The volume will be useful not only to the students of all levels but also to the engineers as well as to the people involved in making decisions in the industry and politics.
The authors have summarized the results obtained in the course of the investigations of the Baltic Sea basin and touched the utilization of the resources, thus enhancing the process of the development of new strategies for monitoring and design of technical devices, including various methods of satellite observation, establishing the research lab for international collaboration, etc.
In fact, the material presented in this title will be of interest for representatives of many disciplines, including marine science, marine ecology and biology, oceanography, who are working in the geographical region in question and equally useful to the people working in other areas. It combines the original studies with the review, using the inter-disciplinary approach.